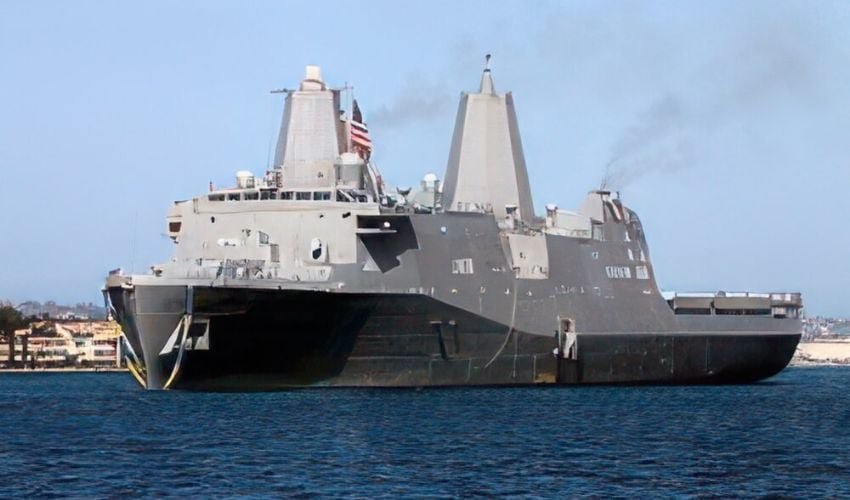
It would not be hyperbole to say that the U.S. Navy has quickly become one of the main adopters of additive manufacturing in the defense sector. We have heard time and time again about successful uses of 3D printing for both boats and submarines, whether as a way to overcome supply chain breakdowns or to ensure that even while at sea it will be possible to access parts. Now there yet another milestone has been achieved. ADDiTEC has announced that the Navy has successfully implemented liquid metal jetting (LMJ) while afloat, printing a high-strength aluminum alloy part.
You may have heard of liquid metal jetting before. The metal 3D printing technology was originally used in Xerox solutions and the U.S. Navy was an early adopter. However, after Xerox announced the end of its additive manufacturing activities, ADDiTEC was the one to save the technology, acquiring the 3D printing business of Xerox as well as the machines. And it is on a containerized ElemX 3D printer using LMJ that parts were made.
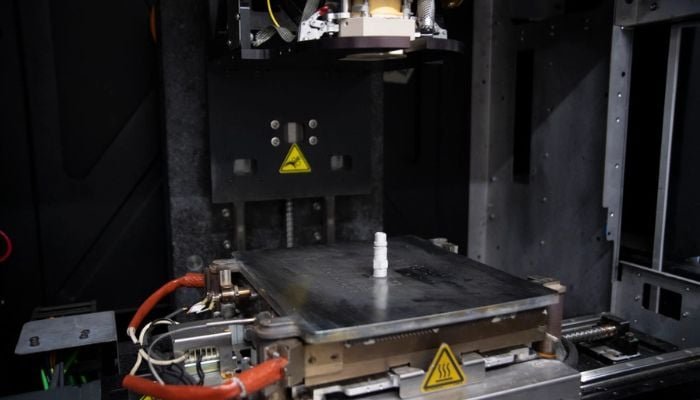
The ElemX 3D printer on the USS San Diego (photo credits: Mass Communication Specialist 1st Class Brandon Woods/U.S. Navy)
Using Metal 3D Printing on the USS San Diego
The U.S. Navy was able to successfully use the 3D printer to produce functional parts afloat while home ported in San Diego. Even more exceptionally, they managed to achieve a milestone by using high-strength aluminum alloys, such as Al-6061. Not only was the process efficient, but it seems that the essential printed parts were evaluated afterwards for quality and performance, and the results showed that they were acceptable and functional for the intended application.
“We are thrilled with the performance of the ElemX 3D printer,” expanded Dr. Garth Hobson, Director of the Consortium for Advanced Manufacturing, Research and Education, at the Naval Postgraduate School, Monterey, California. “The ease of use and the quality of the printed parts exceeded our expectations. This technology represents a significant enhancement in our ability to maintain and repair equipment while at sea.”
The Naval Postgraduate School (NPS) and Consortium for Advanced Manufacturing Research and Education (CAMRE) have been playing a pivotal role in advancing research into the use of AM in naval environments. Before this case, the two were also recently involved in the use of 3D printing in technical exercises and on other ships, such as the USS Essex. They chose to deploy the ElemX printer on the USS San Diego to test how it would perform when using to fabricate critical parts, ultimately hoping to reduce downtime and enable faster repairs for enhanced operational readiness and efficiency. With this press release, it seems that it has been a success.
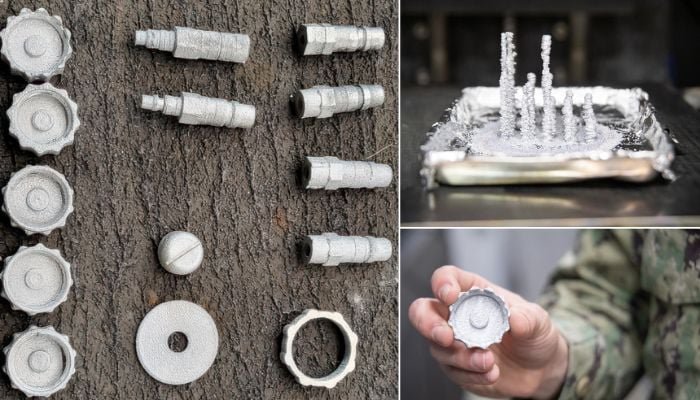
Left: Some of the Aluminum 6061 parts printed with the Elem X (photo credits: ADDiTEC); Other parts made using the ElemX on the USS San Diego (photo credits: Mass Communication Specialist 1st Class Brandon Woods/U.S. Navy)
The ability especially to print high-strength aluminum alloy parts on demand could represent a huge, transformative shift in how the U.S. Navy will be able to manage it resources and address maintenance challenges. ADDiTEC at least hopes that by achieving this milestone, it will be possible to reduce dependency on traditional supply chains, a necessity especially for ships which will often need to spend large amounts of time away from land and especially friendly ports.
What do you think of the use of metal 3D printing on the USS San Diego? Let us know in a comment below or on our LinkedIn, Facebook, and Twitter pages! Don’t forget to sign up for our free weekly newsletter here for the latest 3D printing news straight to your inbox! You can also find all our videos on our YouTube channel.
*Cover: The USS San Diego (photo credits: Staff Sgt. Heidi E. Agostini/United States Marine Corps)